At SAB Aerospace, Product & Quality Assurance (PA/QA) engineers play a pivotal role in enhancing mission success. They ensure the suitability of materials, mechanical parts, electrical components and processes, anticipating future needs and monitoring industry trends.
Verifying compliance with Product Assurance requirements involves providing engineering support and being available for mechanical assembly and integration, addressing any quality issues proactively. Starting from the project specifications, SAB Aerospace’s PA-QA team qualifies flight hardware by performing all the required mechanical tests, in-house when possible or using the major European Test Centres.
All our components and systems go through a battery of rigorous testing.
OUR EXPERTISE
An ESA-registered supplier, SAB Aerospace has emerged as a significant player in the aerospace industry, providing operators with a wealth of expertise and specialisations for space applications.
Our core business is designing and developing mechanical components, systems, subsystems, and mechanisms for satellites and launchers. Our strategic emphasis is on innovations related to microsatellite separation and in-orbit services at the forefront of aerospace technology.
Our involvement in the entire lifecycle of components, from mechanical and thermal design to production, integration, testing, and client support, reflects our comprehensive approach to delivering both reliable and efficient turnkey and made-to-measure space solutions.
We have a wealth of expertise in the following areas:
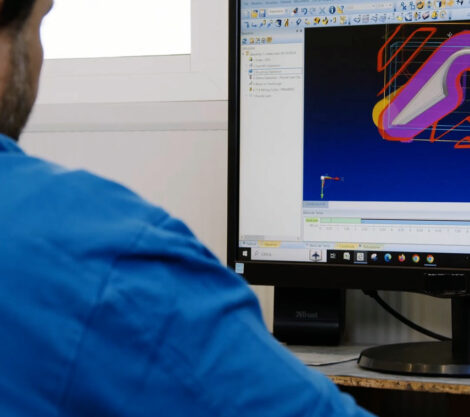
Design
- Designing components, systems, and mechanisms for space applications
- Satellite and launcher component design
- 3D CAD mechanical design
- Electrical design
- Design and construction of MGSE tests
Testing
- Structural analysis
- Thermal analysis
- Space simulation tests
- Analyses and computational simulation
- Vibration and shock testing
- Thermal vacuum tests
- Static strength and stiffness tests
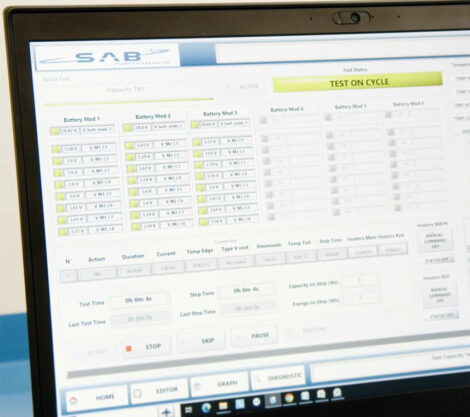
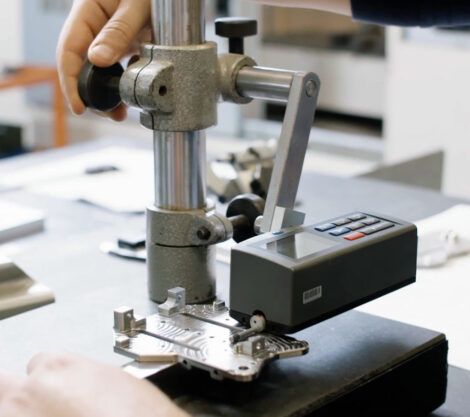
Manufacturing
- Microsatellite separation components
- Electronics, photonics and optics
- Integrated sensors
- Cryogenic components
- Quantum technology manufacturing
- Technologies for space transportation
- Modular batteries
- Launchers, adapters, dispensers and interface rings
- UAV components
- Machined parts
- Composite parts
- MWI baseplates
- Additive manufacturing
Support
- In-orbit services
- Project and test management
- AIT and QA support
- Methods and procedures consultancy
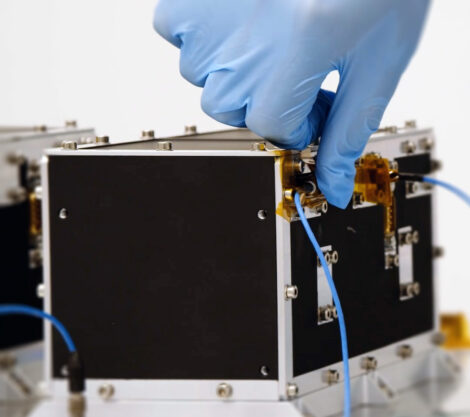
CERTIFICATIONS
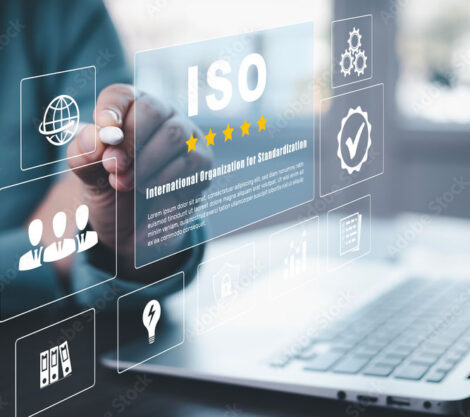
SAB Aerospace operates to the highest levels of precision and quality. Our products and services conform to the most stringent international standards and regulations.
ISO 9001: 2015 Certification
This internationally recognised standard testifies to the effectiveness of our quality management systems.
Clean Room ISO8
We have a certified ISO8 Clean Room facility. This controlled environment guarantees protection against airborne particles, dust, and contaminants, crucial for the integrity of aerospace components.
Audits by ESA, Thales, Ariane Group
We undergo regular audits by leading organisations, including the European Space Agency (ESA), Thales, and ArianeGroup. These audits confirm our compliance with exacting industry standards.
QUALITY SYSTEM
The decision to adopt a Quality Management System at SAB AEROSPACE S.r.l. is motivated by the need to clearly and unambiguously regulate productivity, using a reference document (the Quality Manual) to optimise resource organisation, establish targeted quality goals and therefore reduce the occurrence of non-compliance situations and conditions in technical and commercial relations with customers.
Quality Policy
In addition to fulfilling these primary purposes, we believe that publicizing the Quality Policy can help raise the culture of quality in the people who work at and for the company, involving them in the knowledge and application of its procedures, so that everyone can contribute to reducing waste and defects related to ‘non-quality’ that inevitably cost the company more and add to the image gained ‘in the field’.
The organisation’s goal is therefore to manage all its operations in such a way as to make the staff aware of its aims, assigning clear responsibilities, with a view to a common goal. SAB AEROSPACE S.r.l. specialises in designing, manufacturing and testing aerospace products and has an established reputation in the field for reliability and professionalism. With this in mind, it is aware of the importance of developing increasingly innovative techniques to offer customers a product that is in step with the times and in compliance with safety regulations.
The Policy Guidelines
SAB AEROSPACE S.r.l. is also a company that stands by its customers, listens to their needs and seeks to find the best solution in every field. It is for this reason that the cornerstone of company management is attention to customer requests, needs and any complaints as an element of feedback on the ‘perceived quality’ of the organisation’s operations. This can only be achieved by training and providing information to our personnel, and especially to subcontractors, who become an integral part of the work we do, to make them aware of the company’s goals and the ways to pursue them. It is also essential to pay attention to the observations made by workers who, being in direct contact with operational issues, are able to draw attention to situations that may not otherwise be detected.
The guidelines through which these primary goals are to be achieved can be summarised as follows:
Quality System Review
When special quality requirements arise from information and considerations beyond actual customer need, or when such information is correlated with market or industry trends concerning ‘potentially required specifications’, the primary corporate departments shall discuss the need for suitable quality and development planning in response to the trend during the Quality System Review.
The Management Representative shall continuously update Management on the System’s performance (including through appropriate statistical evaluations of relevant data), and Management shall set out the economic and market strategies accordingly.
Management’s task is therefore to gather all the information that comes in from customers and operators to make improvements to the product or service provided.
In this way, the entire company, working from instructions provided by Management, is able to collaborate with Management itself to be able to provide a reliable service at the quality levels required by the market.