SAB Aerospace develops, produces and qualifies the complex structures of satellites and launchers with thermal hardware ready for the extreme and highly variable temperatures of space.
The company uses traditional and innovative technologies and materials to remain at the forefront of the ever-evolving field of thermal control subsystems.
Thermal Control Subsystems In Brief
The Thermal Control Subsystem (TCS) plays a pivotal role in ensuring that electronic and mechanical systems within a spacecraft operate within their specified temperature ranges, guaranteeing optimal functionality and longevity.
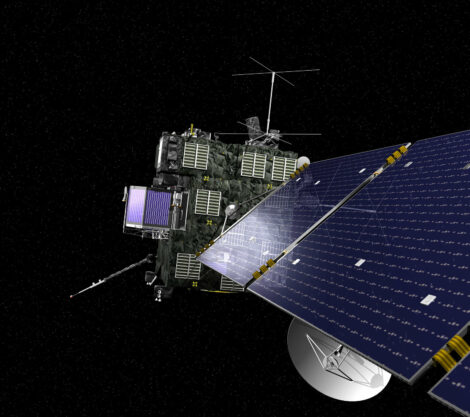
Addressing temperature extremes poses a fundamental challenge for satellite developers in their engineering endeavours. In addition to contending with external thermal stress, spacecraft developers must also manage the heat generated by the spacecraft’s power-generating subsystems. Furthermore, upon launch, as they travel through the atmosphere, payload fairings undergo significant aerodynamic heating.
The aerospace industry continually pushes the boundaries of technology to enhance the performance and reliability of spacecraft and satellites. One critical aspect of this pursuit is developing efficient Thermal Control Subsystems to manage the thermal environment of aerospace components.
Passive thermal control subsystems rely on materials and design elements that naturally dissipate or absorb heat, while active systems incorporate mechanisms to actively control temperatures.
Where We Come In
Space is a harsh environment, with temperatures ranging from extremely cold to scorching hot, depending on the spacecraft’s location and exposure to the sun. Without proper thermal management, electronic components can either freeze or overheat, leading to malfunctions or complete failure.
To address these challenges, SAB engineers are constantly refining and innovating Thermal Control Subsystems to provide precise and reliable temperature regulation.
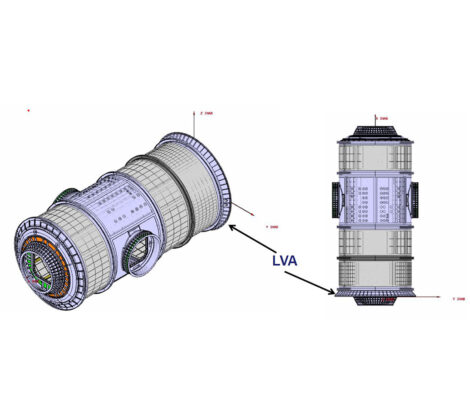
SAB Aerospace provides a comprehensive range of services, beginning with a meticulous analysis of the thermal flux components will be required to tolerate and culminating in the design and qualification of the entire thermal subsystem.
Part of the SAB thermal control subsystem design process is generating TMM and GMM models in ESATAN TMS and Sinda/Fluint and Thermal Desktop for equipment, support structures, mechanisms, and subsystems and thermal analyses. This includes transient and steady-state scenarios from preliminary models to CDR (including acceptance verification of derated components/junction-case temperatures as per ECSS-Q60-11A).
SAB also performs thermal model correlation with TVTC test results and sensitivity analyses and generates input for thermo-elastic analyses for optical payload (input to FEM). The company is also involved in generating and handling thermal IF data for equipment and subsystems (MERAT data) and provides comprehensive thermal reports and document issuance.